por PyMECity.es | 22-04-2025 | Producción
Cinco Claves para una Producción Empresarial Sostenible y Ecológica
La producción sostenible es un enfoque que busca minimizar el impacto ambiental de las empresas mientras se maximiza la eficiencia de recursos. Adoptar prácticas sostenibles no solo beneficia al medio ambiente, sino que también puede mejorar la rentabilidad a largo plazo. Las empresas que implementan estrategias ecológicas suelen experimentar un aumento en la lealtad del cliente y una mejor reputación en el mercado.
Existen varias claves para lograr una producción empresarial sostenible, comenzando por la adopción de diseños ecológicos que optimizan el uso de recursos. Además, la transparencia en las prácticas sostenibles es crucial, ya que permite a los consumidores conocer y confiar en los esfuerzos de la empresa. Implementar un sistema de gestión eficiente, como un ERP, puede facilitar la integración de estas prácticas en las operaciones diarias.
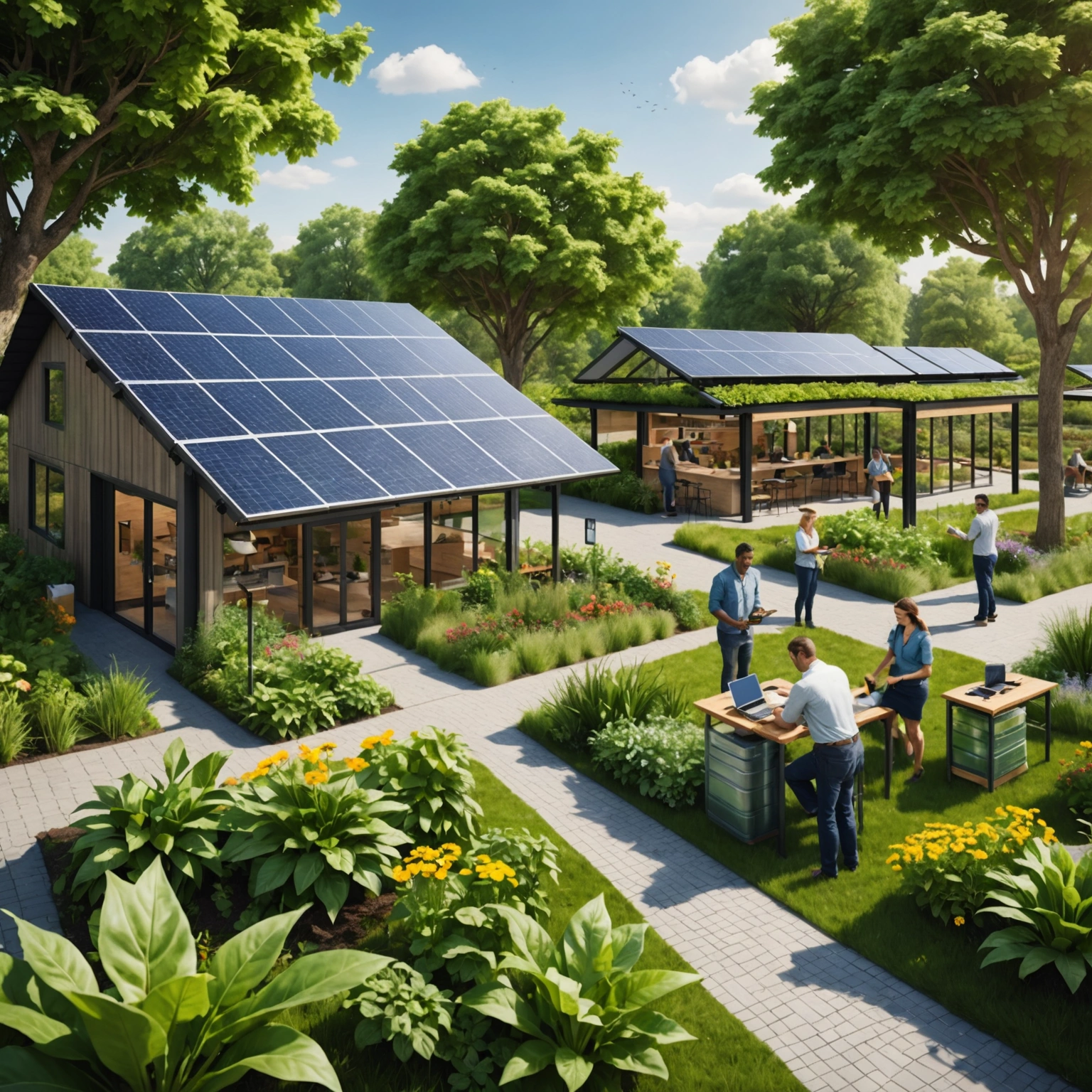
Introducción a la Producción Sostenible
La producción sostenible se ha convertido en un concepto fundamental en el mundo empresarial actual, impulsado por la creciente preocupación por el medio ambiente y los recursos naturales. Este enfoque busca optimizar los procesos productivos mientras se reducen los desechos y se minimiza la huella de carbono. Las empresas que adoptan prácticas sostenibles no solo contribuyen a la conservación del planeta, sino que también pueden acceder a nuevos mercados y oportunidades de negocio.
Implementar la producción sostenible implica repensar cada etapa de la cadena de valor, desde la adquisición de materias primas hasta la distribución de productos. Las empresas deben considerar el ciclo de vida de sus productos y buscar maneras de hacerlos más eficientes y menos perjudiciales para el entorno. Además, la responsabilidad social corporativa se ha vuelto un aspecto esencial, ya que los consumidores valoran cada vez más a las marcas que demuestran un compromiso genuino con la sostenibilidad.
Importancia de la Sostenibilidad en las Empresas
La sostenibilidad en las empresas es crucial para abordar los desafíos ambientales globales que enfrentamos hoy en día. Adoptar prácticas sostenibles permite a las organizaciones reducir su huella ecológica y promover el uso eficiente de los recursos, lo que es vital en un mundo con recursos limitados. Además, las empresas que se comprometen con la sostenibilidad tienden a atraer a un público más consciente y responsable, lo que puede traducirse en un aumento de la lealtad del cliente.
Asimismo, la sostenibilidad se ha convertido en un factor diferencial en la competitividad empresarial. Las empresas que implementan políticas sostenibles a menudo logran disminuir costos operativos a través de la optimización de recursos y la reducción de desechos. También, ser reconocidas como socialmente responsables puede mejorar significativamente la reputación de la marca, facilitando la conexión con inversores y socios comerciales interesados en prácticas éticas y responsables.
Objetivos del Artículo
El principal objetivo de este artículo es proporcionar un marco claro sobre cómo lograr una producción sostenible en las empresas. A través de la exploración de cinco claves fundamentales, se busca equipar a los lectores con las herramientas necesarias para implementar prácticas que beneficien tanto al medio ambiente como a su propio negocio. Cada clave se presenta con ejemplos prácticos, facilitando así la comprensión y la aplicabilidad de los conceptos discutidos.
Además, el artículo tiene como meta destacar la relevancia de la transparencia y la responsabilidad en las operaciones empresariales actuales. Se pretende que los lectores reconozcan la importancia de centrar sus esfuerzos en la creación de valor a largo plazo, en lugar de enfocarse únicamente en beneficios inmediatos. Al abordar estos objetivos, se espera fomentar un cambio positivo en la mentalidad empresarial hacia una gestión ecológica y responsable.
Claves para Lograr una Producción Sostenible
Una de las claves más importantes para lograr una producción sostenible es la adopción de diseños ecológicos. Esto implica reevaluar los procesos de producción para optimizar el uso de recursos y minimizar los desechos generados. Implementar técnicas que prioricen la eficiencia energética y reduzcan el impacto ambiental no solo beneficia al planeta, sino que también puede resultar en ahorros significativos para las empresas.
Otra clave esencial es mantener una transparencia absoluta en las prácticas sostenibles. Las empresas deben comunicar abiertamente sus esfuerzos y logros en sostenibilidad, lo que fortalece la confianza con los consumidores y otros grupos de interés. Además, enfocarse en la economía circular —promoviendo el reciclaje y la recuperación de materiales— contribuye a un modelo de negocio más responsable y resiliente, que puede adaptarse a los cambios del mercado.
1. Adopción de Diseños de Producción Ecológicos
La adopción de diseños de producción ecológicos es fundamental para reducir el impacto ambiental de las empresas. Esto implica evaluar cada etapa del proceso productivo y hacer ajustes que optimicen el uso de recursos como agua, energía y materias primas. Al implementar tecnologías más limpias y métodos de producción innovadores, las empresas pueden minimizar los desechos y mejorar su eficiencia operativa.
Además, los diseños de producción ecológicos fomentan la creación de productos que son más duraderos y fáciles de reciclar. Al considerar el ciclo de vida de los productos, las empresas pueden asegurar que sus operaciones no solo sean rentables, sino que también sean responsables con el medio ambiente. Esta estrategia no solo ayuda a cumplir con regulaciones ambientales, sino que también puede posicionar a las empresas como líderes en sostenibilidad dentro de su sector.
Eficiencia de Recursos
La eficiencia de recursos es un pilar clave en la producción sostenible, ya que se centra en maximizar el uso de insumos mientras se minimizan los desechos generados. Implementar prácticas que optimicen el consumo de energía, agua y materiales no solo reduce costos operativos, sino que también disminuye la huella ecológica de la empresa. Al utilizar tecnologías avanzadas, como la automatización y el monitoreo en tiempo real, las organizaciones pueden identificar áreas de mejora y ajustar sus procesos de manera efectiva.
Además, la eficiencia en el uso de recursos contribuye a la competitividad en un mercado cada vez más consciente de la sostenibilidad. Las empresas que logran optimizar sus recursos suelen destacarse frente a sus competidores, atrayendo a consumidores que valoran el compromiso ambiental. Por lo tanto, invertir en estrategias de eficiencia no solo es beneficioso para el planeta, sino que también puede resultar en una ventaja económica significativa a largo plazo.
Minimización de Residuos
La minimización de residuos es un componente esencial de la producción sostenible, ya que busca reducir la cantidad de desechos generados en cada etapa del proceso productivo. Implementar prácticas como la reducción, la reutilización y el reciclaje puede transformar la forma en que las empresas gestionan sus desechos. Al adoptar un enfoque proactivo hacia la minimización de residuos, las organizaciones no solo cumplen con regulaciones ambientales, sino que también pueden reducir costos asociados a la eliminación de desechos.
Además, fomentar la minimización de residuos puede generar un impacto positivo en la percepción pública de la empresa. Las marcas que demuestran un compromiso genuino con la reducción de residuos tienden a ganar la confianza de los consumidores y a mejorar su reputación en el mercado. Invertir en tecnologías que faciliten la gestión de residuos eficientemente, como sistemas de separación y compostaje, puede ser una estrategia efectiva para avanzar hacia un modelo de negocio más sostenible.
2. Transparencia en las Prácticas Sostenibles
La transparencia en las prácticas sostenibles es fundamental para construir la confianza del consumidor y fortalecer la relación entre la empresa y sus stakeholders. Compartir información clara sobre los esfuerzos y logros en sostenibilidad permite a las organizaciones demostrar su compromiso genuino con el medio ambiente. Esto incluye la divulgación de datos sobre el uso de recursos, la gestión de residuos y las iniciativas de responsabilidad social corporativa.
Además, la transparencia promueve un entorno de rendición de cuentas donde las empresas son responsables de sus acciones y decisiones. Al publicar informes de sostenibilidad y participar en certificaciones reconocidas, las organizaciones pueden establecer estándares claros y accesibles para la evaluación de su desempeño. Este enfoque no solo mejora la credibilidad de la empresa, sino que también puede influir en decisiones de compra de los consumidores más conscientes de la sostenibilidad.
Comunicación Clara con Stakeholders
Una comunicación clara con los stakeholders es vital para el éxito de las prácticas sostenibles de una empresa. Mantener informados a los clientes, proveedores y otros interesados sobre los esfuerzos y logros en sostenibilidad ayuda a construir una relación sólida basada en la confianza y la transparencia. Esto puede lograrse a través de informes periódicos, boletines informativos y actualizaciones en redes sociales que resalten las iniciativas sostenibles de la organización.
Además, la comunicación efectiva fomenta la participación activa de los stakeholders en el proceso de sostenibilidad. Al involucrar a estos grupos en el desarrollo de políticas y estrategias, las empresas pueden obtener valiosos insumos y perspectivas que enriquecen sus prácticas. Esta colaboración no solo mejora la percepción de la empresa, sino que también puede resultar en un impacto positivo en la comunidad y el entorno en el que opera.
Informes de Sostenibilidad
Los informes de sostenibilidad son herramientas clave para que las empresas comuniquen su desempeño en materia de sostenibilidad. Estos documentos detallan las iniciativas, resultados y metas en relación con el medio ambiente, la sociedad y la gobernanza, proporcionando una visión clara de las prácticas sostenibles de la organización. Al elaborar estos informes de manera precisa y transparente, las empresas pueden establecer estándares y expectativas claras tanto para sus operaciones internas como para sus stakeholders.
Además, los informes de sostenibilidad permiten a las empresas medir y evaluar su progreso a lo largo del tiempo. Al incluir métricas e indicadores clave de rendimiento, las organizaciones pueden identificar áreas de mejora y ajustar sus estrategias según sea necesario. Esto no solo fortalece la confianza con los consumidores, sino que también demuestra un compromiso real con la responsabilidad social y ambiental, lo que puede diferenciar a la empresa en un mercado cada vez más competitivo.
3. Creación de Valor a Largo Plazo
La creación de valor a largo plazo es esencial para el crecimiento sostenible de las empresas en el entorno actual. A diferencia de las estrategias que se centran en beneficios inmediatos, este enfoque promueve prácticas que benefician tanto a la organización como a la sociedad. Invertir en sostenibilidad no solo mejora la reputación de la marca, sino que también puede resultar en un aumento significativo de la lealtad del cliente y la satisfacción a largo plazo.
Además, al priorizar la creación de valor a largo plazo, las empresas pueden adaptarse mejor a las tendencias del mercado y a las expectativas cambiantes de los consumidores. Esto incluye la innovación en productos y servicios que no solo cumplen con las demandas actuales, sino que también están alineados con los objetivos de sostenibilidad. Al integrar la sostenibilidad en su modelo de negocio, las organizaciones pueden asegurar su viabilidad y competitividad futura.
Beneficios a Largo Plazo vs. Inmediatos
Los beneficios a largo plazo de la sostenibilidad suelen superar significativamente los beneficios inmediatos, aunque estos últimos puedan parecer más atractivos en un primer momento. Invertir en prácticas sostenibles puede generar ahorros sustanciales en costos operativos, como la reducción de desperdicios y el uso eficiente de recursos. A medida que el mercado se vuelve más consciente de la sostenibilidad, las empresas que priorizan el valor a largo plazo pueden disfrutar de una ventaja competitiva considerable.
Por otro lado, los beneficios inmediatos, como un aumento rápido en las ventas impulsadas por promociones o costos iniciales más bajos, pueden ofrecer resultados temporales. Sin embargo, estas estrategias pueden no ser sostenibles a largo plazo y pueden poner en riesgo la reputación de la marca si no se alinean con prácticas responsables. En contraste, centrarse en la creación de valor a largo plazo construye una base sólida para el crecimiento continuo y la lealtad del cliente, asegurando el éxito futuro de la organización.
Inversión en Sostenibilidad
La inversión en sostenibilidad no solo es esencial para el bienestar del medio ambiente, sino que también representa una oportunidad estratégica para las empresas. Al destinar recursos a prácticas sostenibles, las organizaciones pueden mejorar su eficiencia operativa y reducir costos a largo plazo. Estas inversiones abarcan desde la implementación de tecnologías limpias hasta la optimización de procesos que minimizan el uso de recursos y la generación de desechos.
Además, la inversión en sostenibilidad puede aumentar el atractivo de la empresa para los inversores y los consumidores conscientes. Cada vez más, los inversionistas están buscando empresas que demuestren un compromiso serio con la sostenibilidad, ya que esto puede traducirse en menor riesgo y mayores retornos a largo plazo. Asimismo, los consumidores prefieren marcas que se alinean con sus valores, lo que puede resultar en un aumento de la lealtad y la satisfacción del cliente.
4. Implementación de la Economía Circular
La implementación de la economía circular es un enfoque revolucionario que busca redefinir la forma en que las empresas gestionan sus recursos y productos. En lugar de seguir un modelo lineal de «tomar, hacer y desechar», este enfoque promueve la recuperación y reutilización de materiales, cerrando el ciclo de vida de los productos. Al adoptar prácticas de economía circular, las empresas pueden reducir su huella ecológica y minimizar el desperdicio, al mismo tiempo que crean nuevos flujos de ingresos a partir de materiales reciclados.
Además, la economía circular fomenta la innovación en el diseño de productos y servicios, incentivando a las empresas a pensar en soluciones más sostenibles desde el principio. Esto incluye el desarrollo de productos que sean más duraderos y fáciles de reciclar, así como la implementación de modelos de negocio que prioricen el servicio sobre la propiedad. Al hacerlo, las organizaciones no solo mejoran su desempeño ambiental, sino que también pueden atraer a un público cada vez más consciente de la sostenibilidad y la responsabilidad social.
Principios de Reciclaje y Recuperación
Los principios de reciclaje y recuperación son fundamentales en la economía circular, ya que buscan maximizar el uso de materiales y minimizar el desperdicio. El reciclaje implica la transformación de materiales desechados en nuevos productos, lo que no solo reduce la demanda de recursos naturales, sino que también disminuye la cantidad de desechos que terminan en vertederos. La recuperación, por otro lado, se refiere a la recolección y procesamiento de materiales para su reutilización, contribuyendo así a un ciclo de vida más sostenible para los productos.
Implementar estos principios requiere un cambio en la mentalidad empresarial y un compromiso con la sostenibilidad a largo plazo. Las empresas pueden adoptar prácticas que faciliten el reciclaje, como el diseño de productos que sean fácilmente desmontables y reciclables. Además, fomentar la educación y la conciencia entre los consumidores sobre la importancia del reciclaje y la recuperación es crucial para lograr una participación activa y efectiva en estas iniciativas.
Rediseño de Productos para la Sostenibilidad
El rediseño de productos para la sostenibilidad es un enfoque esencial que permite a las empresas minimizar su impacto ambiental a lo largo del ciclo de vida del producto. Esto implica considerar aspectos como la selección de materiales reciclables, la reducción de empaques y la optimización de la producción para disminuir el consumo de recursos. Al implementar un diseño sostenible, las organizaciones no solo contribuyen al cuidado del medio ambiente, sino que también pueden mejorar la eficiencia y reducir costos.
Además, el rediseño para la sostenibilidad fomenta la innovación al motivar a las empresas a desarrollar soluciones creativas que cumplan con las expectativas de los consumidores modernos. Esto incluye la creación de productos que sean duraderos, fácilmente reparables y que ofrezcan la posibilidad de descomponerse al final de su vida útil. Al centrar el proceso de diseño en la sostenibilidad, las empresas pueden posicionarse como líderes en su sector y atraer a un público que valora la responsabilidad ambiental.
5. Mejora de la Reputación de la Marca
La mejora de la reputación de la marca es uno de los beneficios más destacados de adoptar prácticas sostenibles. Las empresas que demuestran un compromiso genuino con la sostenibilidad suelen ganar la confianza de los consumidores, lo que se traduce en una mayor lealtad y apoyo a largo plazo. Al comunicar efectivamente sus esfuerzos en sostenibilidad, las organizaciones pueden posicionarse favorablemente en la mente de los clientes y diferenciarse de la competencia.
Además, una buena reputación en sostenibilidad puede atraer a inversionistas y socios comerciales que valoran la responsabilidad social y ambiental. Las marcas con una sólida imagen de sostenibilidad no solo son vistas como más atractivas, sino que también pueden beneficiarse de un mayor acceso a recursos y oportunidades de colaboración. En un mercado donde los consumidores son cada vez más conscientes de sus elecciones de compra, la reputación de la marca puede influir significativamente en su decisión final.
Construcción de Confianza con el Consumidor
Construir confianza con el consumidor es un aspecto crucial para el éxito de cualquier marca, especialmente en el contexto de la sostenibilidad. Las empresas que son transparentes en sus prácticas sostenibles y cumplen con sus promesas generan un sentido de credibilidad que atrae a los consumidores. Al demostrar un compromiso real con la responsabilidad social y ambiental, las marcas pueden establecer relaciones sólidas y duraderas con sus clientes.
Además, la comunicación abierta sobre las iniciativas sostenibles refuerza la confianza del consumidor y fomenta la lealtad. Cuando los consumidores perciben que una empresa se esfuerza por ser sostenible, es más probable que opten por sus productos o servicios en lugar de los de la competencia. Este enfoque no solo mejora la reputación de la marca, sino que también puede resultar en un aumento en las ventas y en la satisfacción general del cliente.
Impacto del Compromiso Genuino con la Sostenibilidad
El compromiso genuino con la sostenibilidad tiene un impacto significativo en la percepción de la marca por parte del consumidor. Cuando una empresa se dedica a prácticas sostenibles de manera auténtica, se establece como un líder en su sector, lo que puede resultar en una mayor lealtad de los clientes y una mejor reputación. Este tipo de compromiso no solo mejora la imagen de la marca, sino que también puede atraer a un público más amplio que valora la responsabilidad ambiental.
Además, las empresas que demuestran un verdadero compromiso con la sostenibilidad tienden a experimentar beneficios económicos tangibles. La implementación de prácticas sostenibles puede llevar a la reducción de costos operativos, así como a la apertura de nuevas oportunidades de negocio en mercados emergentes que priorizan la sostenibilidad. En última instancia, este impacto positivo refuerza la idea de que la sostenibilidad no es solo una tendencia, sino una estrategia empresarial esencial para el éxito a largo plazo.
Herramientas para Optimizar la Producción Sostenible
Existen diversas herramientas que las empresas pueden utilizar para optimizar su producción sostenible, comenzando con software de gestión de recursos. Estas plataformas permiten a las organizaciones monitorear y analizar el uso de materiales, energía y otros recursos, facilitando la identificación de áreas de mejora. Al implementar estas soluciones tecnológicas, las empresas pueden reducir costos y mejorar su eficiencia operativa de manera significativa.
Otro conjunto de herramientas clave son las técnicas de análisis de ciclo de vida, que ayudan a las empresas a evaluar el impacto ambiental de sus productos desde la producción hasta la disposición final. Estas técnicas permiten identificar oportunidades para reducir desechos y optimizar el uso de recursos a lo largo del ciclo de vida del producto. Además, el uso de tecnologías de automatización y monitoreo en tiempo real puede mejorar la sostenibilidad, permitiendo ajustes inmediatos en los procesos productivos para minimizar el impacto ambiental.
Uso de Sistemas de Gestión Empresarial (ERP)
Los sistemas de gestión empresarial (ERP) son herramientas fundamentales para optimizar la producción sostenible en las organizaciones. Estos sistemas integran diferentes procesos y funciones de la empresa, permitiendo un acceso centralizado a datos clave sobre inventarios, finanzas y producción. Al proporcionar información en tiempo real, los ERP facilitan la toma de decisiones informadas que pueden mejorar la eficiencia y reducir el desperdicio.
Además, los sistemas ERP son esenciales para el cumplimiento de normativas de sostenibilidad y la generación de informes de desempeño ambiental. Con la capacidad de rastrear el uso de recursos y las emisiones generadas, estos sistemas ayudan a las empresas a identificar áreas que requieren mejoras y a implementar prácticas más sostenibles. Al adoptar un ERP, las organizaciones no solo optimizan sus operaciones, sino que también se posicionan como líderes en sostenibilidad dentro de su sector.
Beneficios del ERP en la Sostenibilidad
Los sistemas ERP ofrecen múltiples beneficios en la sostenibilidad al mejorar la eficiencia operativa y reducir el uso de recursos. Al integrar datos de diferentes departamentos, las empresas pueden identificar áreas de desperdicio y oportunidades para optimizar procesos, lo que se traduce en un menor impacto ambiental. Además, el acceso a información en tiempo real permite a las organizaciones tomar decisiones más informadas y ágiles en cuanto a la gestión de sus recursos.
Otro beneficio clave de los ERP es su capacidad para facilitar la generación de informes de sostenibilidad. Estos sistemas permiten a las empresas rastrear su desempeño ambiental y cumplir con las normativas vigentes, lo que puede mejorar su reputación y credibilidad en el mercado. Al documentar y analizar el uso de recursos y las emisiones, las organizaciones pueden establecer objetivos claros y medibles para avanzar hacia una operación más sostenible.
Ejemplos de Implementación de ERP
Un ejemplo notable de implementación de ERP se puede observar en la industria manufacturera, donde empresas como Boeing utilizan sistemas ERP para gestionar su cadena de suministro y optimizar la producción. Al integrar datos de diferentes fuentes, Boeing puede mejorar la eficiencia en la gestión de inventarios y reducir costos, lo que a su vez contribuye a prácticas más sostenibles. Este enfoque permite a la compañía minimizar el desperdicio de materiales y asegurar que se utilicen solo los recursos necesarios en cada etapa del proceso.
Otro caso es el de la empresa de alimentos Unilever, que ha implementado un sistema ERP para ayudar a gestionar su compleja red de operaciones a nivel global. Gracias a esta herramienta, Unilever puede rastrear el uso de energía y recursos en sus fábricas, permitiendo la identificación de áreas donde se puede mejorar la sostenibilidad. Además, el sistema ERP facilita la generación de informes que ayudan a la empresa a cumplir con sus objetivos de responsabilidad social y ambiental.
por PyMECity.es | 18-04-2025 | Ninguna
Transformando el Futuro: Tendencias de Sostenibilidad para 2024
En el año 2024, las empresas se enfrentarán a un panorama cambiante impulsado por la necesidad de adoptar prácticas de sostenibilidad más rigurosas. La creciente presión de los consumidores, inversores y reguladores demandará una mayor transparencia y rendición de cuentas en las operaciones comerciales. Las organizaciones que no se adapten a estas tendencias corren el riesgo de quedarse atrás en un mercado cada vez más consciente de su impacto ambiental y social.
Una de las tendencias más significativas será la integración de la tecnología Climate-Positive, que busca no solo reducir el impacto ambiental, sino generar un impacto neto positivo en el clima. Además, se anticipa un aumento en los empleos relacionados con la sostenibilidad, lo que reflejará un cambio en la cultura empresarial hacia prácticas más responsables y éticas. Con el enfoque en las emisiones de Alcance 3, las empresas deberán prestar atención a su cadena de suministro y a cómo sus operaciones afectan al medio ambiente en su totalidad.

Tendencias de Sostenibilidad para 2024
Las tendencias de sostenibilidad para 2024 están marcando un cambio significativo en la forma en que las empresas operan. Con un enfoque creciente en la tecnología Climate-Positive, las organizaciones están buscando no solo reducir su huella ambiental, sino también crear un impacto positivo en el clima. Este enfoque innovador es clave para diferenciarse en un mercado cada vez más competitivo y consciente de las prácticas sostenibles.
Además, la regulación en materia de sostenibilidad está experimentando un cambio drástico, con la implementación de directrices como el CSRD que exige a las empresas una mayor responsabilidad en sus informes de sostenibilidad. La presión para evitar el greenwashing también está aumentando, ya que los consumidores son más críticos y buscan autenticidad en las afirmaciones de sostenibilidad. Estas tendencias subrayan la importancia de una estrategia sólida y bien comunicada en el ámbito de la sostenibilidad para las empresas modernas.
Adaptación al Entorno Empresarial en Evolución
La adaptación al entorno empresarial es esencial en un mundo donde los cambios son constantes y rápidos. Las empresas deben estar atentas a las tendencias del mercado y a las demandas de los consumidores para mantenerse competitivas. Ignorar estos cambios puede resultar en la pérdida de oportunidades y en un descenso en la relevancia del negocio.
Para enfrentar estos desafíos, las organizaciones están incorporando prácticas de innovación continua y flexibilidad en sus modelos de negocio. Esto incluye la implementación de tecnologías emergentes que facilitan la toma de decisiones y mejoran la eficiencia operativa. Al fomentar una cultura que valore la adaptabilidad, las empresas pueden navegar con éxito en un entorno empresarial en constante evolución.
Desafíos Ambientales y Sociales
Los desafíos ambientales y sociales son cada vez más evidentes en el contexto actual, donde los efectos del cambio climático se sienten en distintas partes del mundo. La escasez de recursos naturales, la contaminación y la pérdida de biodiversidad son problemas que requieren atención urgente por parte de las empresas y gobiernos. Además, la desigualdad social y económica también plantea un desafío significativo que impacta en el desarrollo sostenible.
Las empresas deben enfrentar la presión de adaptarse a estos desafíos mediante la implementación de prácticas responsables y sostenibles. Esto incluye la adopción de estrategias que minimicen su huella ecológica y promuevan la justicia social. Al abordar estos problemas de manera proactiva, las organizaciones pueden contribuir a un futuro más equilibrado y saludable para todos.
Tecnología Climate-Positive como Motor de Cambio
La tecnología Climate-Positive se presenta como una solución innovadora para abordar los retos ambientales actuales. Este enfoque no solo busca reducir las emisiones de carbono, sino también generar un impacto positivo en el medio ambiente al capturar más carbono del que se emite. Las empresas que adoptan esta tecnología están a la vanguardia de un movimiento que promueve la sostenibilidad y la responsabilidad ambiental.
Entre las herramientas clave de esta tecnología se encuentran las energías renovables, la eficiencia energética y las prácticas de gestión de residuos. Al integrar estas soluciones, las organizaciones pueden transformar sus operaciones y contribuir a la creación de un mundo más sostenible. Además, la implementación de tecnologías Climate-Positive puede mejorar la reputación de la marca y atraer a consumidores que valoran el compromiso con el medio ambiente.
Definición y Beneficios de la Tecnología Climate-Positive
La tecnología Climate-Positive se refiere a un conjunto de innovaciones y prácticas que no solo reducen la huella de carbono, sino que también contribuyen a la captura y eliminación de dióxido de carbono de la atmósfera. Este enfoque va más allá de la sostenibilidad tradicional, buscando crear un impacto neto positivo en el medio ambiente. Al adoptar tecnologías Climate-Positive, las empresas pueden posicionarse como líderes en la lucha contra el cambio climático.
Entre los beneficios de esta tecnología se encuentran la mejora de la eficiencia energética y la reducción de costos operativos a largo plazo. Implementar soluciones que generan energía limpia y renovable no solo disminuye las emisiones, sino que también puede ofrecer ventajas competitivas en un mercado cada vez más consciente de la sostenibilidad. Además, las empresas que se comprometen con un enfoque Climate-Positive pueden atraer a un público más amplio, incluyendo a consumidores que valoran el compromiso ambiental.
Ejemplos de Innovaciones en el Mercado
Una de las innovaciones más destacadas en el mercado es el uso de paneles solares integrados en edificios, lo que permite generar energía limpia y reducir la dependencia de fuentes fósiles. Estos sistemas no solo contribuyen a la sostenibilidad, sino que también ofrecen beneficios económicos al disminuir las facturas de electricidad. Además, algunas empresas están implementando tecnologías de almacenamiento de energía que permiten utilizar la energía solar incluso durante la noche o en días nublados.
Otro ejemplo significativo es el desarrollo de vehículos eléctricos que han transformado la industria automotriz. Estos autos no solo reducen las emisiones de gases de efecto invernadero, sino que también promueven un estilo de vida más sostenible y consciente. Compañías innovadoras están trabajando en la creación de infraestructura de carga más accesible, facilitando así la adopción masiva de esta tecnología entre los consumidores.
Aumento de Empleos en el Ámbito de la Sostenibilidad
El aumento de empleos en el ámbito de la sostenibilidad se ha convertido en una tendencia notable en los últimos años. Con un creciente enfoque en prácticas empresariales responsables, se están creando nuevos roles que abarcan desde especialistas en energías renovables hasta gerentes de sostenibilidad. Este cambio no solo responde a la demanda del mercado, sino que también refleja un cambio cultural hacia la responsabilidad ambiental en el lugar de trabajo.
Además, los puestos tradicionales están siendo transformados para incluir un enfoque en la sostenibilidad, lo que permite que áreas como el marketing y las finanzas incorporen principios sostenibles en sus estrategias. Empresas de diferentes sectores están buscando profesionales que no solo tengan habilidades técnicas, sino que también compartan una visión comprometida con la sostenibilidad. Este fenómeno no solo beneficia a las organizaciones, sino que también empodera a los empleados al alinear sus trabajos con valores que importan.
Nuevos Roles y Oportunidades Laborales
El crecimiento del sector de la sostenibilidad ha dado lugar a una variedad de nuevos roles laborales que antes no existían. Desde especialistas en gestión ambiental hasta analistas de sostenibilidad, estas posiciones están diseñadas para abordar los desafíos actuales y futuros de las empresas. A medida que más organizaciones reconocen la importancia de ser sostenibles, la demanda de profesionales capacitados en este ámbito sigue en aumento.
Además, la intersección de la tecnología y la sostenibilidad ha creado oportunidades en áreas como la inteligencia artificial y el análisis de datos. Los expertos en estas tecnologías están trabajando para desarrollar soluciones que mejoren la eficiencia energética y reduzcan el impacto ambiental. Este enfoque multifacético brinda a los profesionales la oportunidad de combinar sus habilidades técnicas con un compromiso genuino hacia un futuro más sostenible.
Transformación de Puestos Tradicionales
La transformación de puestos tradicionales es una tendencia creciente en el ámbito laboral, impulsada por la necesidad de incorporar prácticas más sostenibles. Por ejemplo, los roles en recursos humanos ahora incluyen la promoción de la diversidad y la inclusión, así como la creación de un entorno de trabajo que fomente la sostenibilidad. Esta evolución permite que las empresas no solo cumplan con regulaciones, sino que también se alineen con las expectativas de los empleados y la sociedad.
Asimismo, las funciones en el departamento de marketing están cambiando para enfatizar el compromiso con la sostenibilidad en sus campañas. Los especialistas en marketing ahora deben ser capaces de comunicar de manera efectiva los esfuerzos de sostenibilidad de sus organizaciones, utilizando narrativas que resalten el impacto positivo en el medio ambiente. Esta adaptación no solo mejora la imagen de la marca, sino que también genera una mayor conexión con los consumidores que valoran la responsabilidad ambiental.
Regulaciones y Transparencia en Sostenibilidad
Las regulaciones en sostenibilidad están tomando un papel cada vez más relevante en el entorno empresarial actual. Directivas como el Corporate Sustainability Reporting Directive (CSRD) exigen a las empresas ser más transparentes en sus informes sobre prácticas ambientales y sociales. Esta normativa no solo busca mejorar la rendición de cuentas, sino que también impulsa a las organizaciones a evaluar su impacto a largo plazo en el medio ambiente y la sociedad.
La presión por cumplir con estas regulaciones ha llevado a muchas empresas a revisar y mejorar sus prácticas de divulgación. Los consumidores y los inversores buscan cada vez más información clara y verificable sobre el compromiso de las empresas con la sostenibilidad. Al adoptar un enfoque proactivo en la transparencia, las organizaciones no solo cumplen con las regulaciones, sino que también fortalecen su reputación y construyen confianza con sus stakeholders.
Preparación para el CSRD
La preparación para el CSRD es fundamental para que las empresas puedan cumplir con las nuevas exigencias de informes de sostenibilidad. Este reglamento europeo exige a las organizaciones no solo reportar sobre su impacto ambiental, sino también sobre aspectos sociales y de gobernanza. Para cumplir con esta normativa, las empresas deben establecer sistemas que recojan y analicen datos relevantes de manera transparente y eficaz.
Además, la implementación del CSRD implica un cambio en la cultura organizacional, ya que requiere el compromiso de todos los niveles de la empresa. La formación y la sensibilización de los empleados son esenciales para garantizar que todos comprendan la importancia de la sostenibilidad en sus funciones diarias. Al adoptar un enfoque integral hacia la sostenibilidad, las empresas no solo se preparan para cumplir con el CSRD, sino que también mejoran su reputación y competitividad en el mercado.
Divulgaciones Obligatorias y su Importancia
Las divulgaciones obligatorias son un componente clave en la nueva era de la sostenibilidad empresarial, ya que garantizan que las organizaciones informen de manera precisa sobre su impacto ambiental y social. Estas divulgaciones permiten a los inversores y consumidores tomar decisiones informadas al evaluar el compromiso de una empresa con prácticas sostenibles. Además, la transparencia en estas comunicaciones ayuda a construir la confianza en la marca y a fortalecer las relaciones con los stakeholders.
La importancia de las divulgaciones radica también en que ofrecen una visión más clara sobre cómo las empresas están abordando los retos del cambio climático y la responsabilidad social. Al cumplir con estas obligaciones, las organizaciones pueden mitigar el riesgo de greenwashing, un fenómeno que se ha vuelto común en el mercado. Esto no solo les permite alinearse con las expectativas regulatorias, sino que también demuestra un auténtico compromiso con la sostenibilidad.
Escrutinio del Greenwashing
El escrutinio del greenwashing ha aumentado significativamente en los últimos años, a medida que los consumidores se vuelven más críticos y exigentes con respecto a las afirmaciones de sostenibilidad de las empresas. Este fenómeno se refiere a las prácticas engañosas donde las organizaciones se presentan como ambientalmente responsables sin realizar cambios significativos en sus operaciones. La creciente atención pública a estas tácticas ha llevado a un mayor deseo de transparencia y autenticidad en las comunicaciones de sostenibilidad.
Las regulaciones también están evolucionando para abordar el greenwashing, estableciendo directrices claras sobre lo que constituye una afirmación sostenible válida. Las empresas ahora enfrentan un mayor riesgo de consecuencias legales si no pueden respaldar sus afirmaciones con datos verificables y acciones concretas. Este escrutinio no solo protege a los consumidores, sino que también impulsa a las empresas a adoptar prácticas más genuinas y efectivas en su camino hacia la sostenibilidad.
Integración de la Sostenibilidad en el Balance Empresarial
La integración de la sostenibilidad en el balance empresarial se está convirtiendo en un elemento esencial para las organizaciones modernas. Este enfoque implica que las empresas no solo se concentren en sus resultados financieros, sino que también consideren su impacto en el entorno social y ambiental. Al adoptar esta perspectiva holística, las organizaciones pueden identificar oportunidades para mejorar su desempeño y contribuir a un futuro más sostenible.
Además, la sostenibilidad integrada permite a las empresas gestionar mejor los riesgos asociados con el cambio climático y otros desafíos ambientales. Esta estrategia no solo ayuda a cumplir con las expectativas reguladoras y de los consumidores, sino que también puede mejorar la reputación de la empresa y fomentar la lealtad entre los clientes. La conexión entre sostenibilidad y rentabilidad se está volviendo cada vez más clara, lo que impulsa a las organizaciones a hacer de la sostenibilidad un pilar fundamental de su modelo de negocio.
Relación entre Sostenibilidad y Finanzas
La relación entre sostenibilidad y finanzas se está volviendo cada vez más relevante en el mundo empresarial actual. Las organizaciones que integran prácticas sostenibles en sus operaciones no solo contribuyen positivamente al medio ambiente, sino que también suelen experimentar una mejora en su rentabilidad a largo plazo. Al reducir costos operativos a través de la eficiencia energética y la gestión de recursos, las empresas pueden lograr un impacto financiero significativo.
Además, los inversores están prestando mayor atención a las prácticas de sostenibilidad al evaluar el valor de una empresa. Las organizaciones que demuestran un compromiso sólido con la sostenibilidad tienden a atraer capital y a obtener financiamiento más fácilmente, ya que los inversores buscan minimizar riesgos relacionados con la regulación ambiental y la reputación. Esta tendencia refuerza la idea de que la sostenibilidad no es solo una responsabilidad social, sino también una estrategia financiera inteligente.
Enfoque en Emisiones de Alcance 3
El enfoque en emisiones de Alcance 3 es crucial para que las empresas comprendan y gestionen su impacto ambiental de manera integral. Estas emisiones incluyen las generadas por actividades que ocurren en la cadena de suministro, así como las asociadas al uso y disposición de sus productos. Al abordar este aspecto, las organizaciones pueden identificar oportunidades para reducir su huella de carbono y mejorar la sostenibilidad en toda su operación.
Sin embargo, medir y gestionar las emisiones de Alcance 3 puede resultar un desafío, ya que dependen de múltiples factores externos y de terceros. Las empresas deben colaborar con proveedores y socios para obtener datos precisos y desarrollar estrategias efectivas que minimicen estas emisiones. Esta colaboración no solo ayuda a las organizaciones a cumplir con las regulaciones ambientales, sino que también fortalece las relaciones comerciales y promueve una cultura de sostenibilidad compartida.
Inteligencia Artificial como Herramienta para la Sostenibilidad
La inteligencia artificial se está convirtiendo en una herramienta fundamental para impulsar la sostenibilidad en diversas industrias. A través del análisis de grandes volúmenes de datos, la IA puede identificar patrones y tendencias que ayudan a las empresas a optimizar sus operaciones y reducir su huella ambiental. Desde la gestión eficiente de recursos hasta la predicción de demandas, la inteligencia artificial ofrece soluciones innovadoras que facilitan un enfoque más sostenible.
Además, la IA puede contribuir a la mejora de procesos en la cadena de suministro, optimizando el uso de materiales y energía. Por ejemplo, algoritmos avanzados pueden ayudar a las organizaciones a minimizar el desperdicio y a mejorar la logística, lo que a su vez reduce las emisiones de gases de efecto invernadero. Al integrar la inteligencia artificial en sus estrategias, las empresas no solo mejoran su eficiencia, sino que también se posicionan como líderes en la transformación sostenible.
Aplicaciones de la IA en Prácticas Sostenibles
Las aplicaciones de la IA en prácticas sostenibles son diversas y están revolucionando la forma en que las empresas operan. Por ejemplo, en el sector de la energía, la inteligencia artificial se utiliza para predecir la demanda y optimizar la producción de energías renovables, como la solar y eólica. Estas tecnologías permiten a las organizaciones ajustar su oferta en tiempo real, maximizando la eficiencia y reduciendo el desperdicio de recursos.
Otro ámbito en el que la IA está haciendo una diferencia significativa es en la gestión de residuos. A través del análisis de datos, la inteligencia artificial puede identificar las tendencias de reciclaje y optimizar las rutas de recolección, lo que minimiza el uso de combustible y reduce las emisiones. Asimismo, la IA ayuda a las empresas a desarrollar productos más sostenibles al analizar el ciclo de vida de los materiales y sugerir alternativas menos perjudiciales para el medio ambiente.
Desafíos y Consideraciones Éticas
Los desafíos y consideraciones éticas en el uso de la inteligencia artificial para la sostenibilidad son aspectos cruciales que deben ser abordados. Uno de los principales retos es garantizar que los algoritmos utilizados sean transparentes y justos, evitando sesgos que puedan perjudicar a ciertos grupos o comunidades. La falta de diversidad en los datos puede llevar a decisiones que no reflejan adecuadamente las necesidades de la población y, por ende, socavar los objetivos de sostenibilidad.
Además, la implementación de la IA plantea interrogantes sobre la privacidad de los datos y la seguridad, ya que la recopilación y el análisis de grandes volúmenes de información pueden comprometer la información personal de los usuarios. Las empresas deben ser responsables en el manejo de estos datos, asegurando que se utilicen de manera ética y conforme a las normativas vigentes. Al abordar estos desafíos éticos, las organizaciones pueden maximizar el potencial de la inteligencia artificial mientras construyen confianza con sus stakeholders.
por PyMECity.es | 14-04-2025 | Producción
Costos de Producción: Clave para la Rentabilidad Empresarial
Los costos de producción son un elemento fundamental en la estructura financiera de cualquier empresa. Estos costos, que incluyen tanto los gastos directos como indirectos, son la base sobre la cual se determina la rentabilidad de una organización. Comprender cómo se clasifican y gestionan puede marcar la diferencia entre el éxito y el fracaso en un mercado cada vez más competitivo.
La correcta estimación y gestión de los costos de producción no solo afecta la rentabilidad, sino también la competitividad en el mercado. Al clasificar los costos en directos, como materias primas y mano de obra, e indirectos, como mantenimiento y administración, las empresas pueden identificar áreas de mejora. Esto permite optimizar recursos y maximizar beneficios, asegurando que cada inversión realizada contribuya efectivamente al crecimiento del negocio.

1. Introducción a los Costos de Producción
Los costos de producción son esenciales para entender la salud financiera de cualquier empresa que fabrique bienes o preste servicios. Estos costos abarcan todos los gastos necesarios para llevar a cabo la producción, desde la adquisición de materias primas hasta el pago de salarios. Al tener una visión clara de estos gastos, las empresas pueden tomar decisiones más informadas y estratégicas.
Existen dos categorías principales dentro de los costos de producción: los costos directos e indirectos. Los costos directos se relacionan directamente con la producción, como la mano de obra y los materiales, mientras que los costos indirectos abarcan gastos como el mantenimiento y la administración. Esta clasificación es crucial para una gestión eficiente y para la optimización de recursos en cualquier organización.
1.1 Definición de Costos de Producción
Los costos de producción se refieren a todos los gastos relacionados con la fabricación de bienes o la prestación de servicios. Estos costos son fundamentales para calcular el precio de venta y determinar la rentabilidad de una empresa. Entender cómo se componen estos costos permite a las organizaciones planificar de manera más efectiva y mejorar su eficiencia operativa.
Una correcta definición de costos de producción implica considerar tanto los gastos fijos como los variables. Los gastos fijos, como el alquiler de instalaciones, no cambian con el nivel de producción, mientras que los variables, como las materias primas, fluctúan según la cantidad producida. Esta dualidad en los costos es esencial para la toma de decisiones estratégicas dentro de las empresas.
1.2 Importancia en el Contexto Empresarial
La importancia de los costos de producción en el contexto empresarial radica en su influencia directa sobre la rentabilidad. Un control adecuado de estos costos permite a las empresas establecer precios competitivos y maximizar sus márgenes de beneficio. Además, una gestión efectiva de los costos contribuye a la sostenibilidad y al crecimiento a largo plazo de la organización.
Entender los costos de producción también es crucial para la toma de decisiones estratégicas. Las empresas que analizan sus costos pueden identificar áreas de mejora, optimizar procesos y reducir gastos innecesarios. Esto no solo mejora la eficiencia operativa, sino que también fortalece la posición competitiva en el mercado.
2. Clasificación de Costos de Producción
La clasificación de costos de producción es fundamental para una gestión financiera efectiva dentro de las empresas. Generalmente, se dividen en dos categorías principales: costos directos e indirectos. Esta distinción permite a las organizaciones entender mejor cómo se distribuyen sus gastos y tomar decisiones informadas sobre la asignación de recursos.
Los costos directos son aquellos que se pueden atribuir directamente a la producción de bienes o servicios, como las materias primas y la mano de obra. Por otro lado, los costos indirectos, como el mantenimiento y la administración, no pueden ser asignados a un producto específico. Esta clasificación ayuda a las empresas a identificar áreas de mejora y a ajustar sus estrategias de reducción de costos.
2.1 Costos Directos
Los costos directos son aquellos gastos que se pueden atribuir de manera clara y específica a la producción de bienes o servicios. Esto incluye elementos como la materia prima utilizada en la fabricación y la mano de obra directa involucrada en el proceso productivo. Al conocer estos costos, las empresas pueden determinar con precisión el costo de producción de cada unidad, lo que es esencial para establecer precios adecuados.
Además de la materia prima y la mano de obra, otros ejemplos de costos directos pueden incluir herramientas y equipos utilizados exclusivamente en la producción. La identificación y gestión de estos costos son fundamentales para mejorar la eficiencia operativa y aumentar los márgenes de beneficio. Al reducir costos directos sin comprometer la calidad, las empresas pueden mejorar significativamente su competitividad en el mercado.
2.1.1 Materias Primas
Las materias primas son los insumos básicos que se utilizan en la producción de bienes y son un componente crítico de los costos directos. Estos materiales pueden variar significativamente según la industria, desde metales y plásticos en la manufactura hasta ingredientes alimentarios en la cocina. La gestión eficiente de las materias primas no solo afecta los costos, sino que también influye en la calidad del producto final.
El costo de las materias primas puede estar sujeto a fluctuaciones en el mercado, lo que hace esencial para las empresas monitorear las tendencias y establecer relaciones sólidas con proveedores confiables. Además, optimizar el uso de estos materiales ayuda a minimizar el desperdicio y mejorar la sostenibilidad en el proceso de producción. Con una adecuada planificación y control, las empresas pueden reducir costos y mejorar su rentabilidad.
2.1.2 Mano de Obra
La mano de obra se refiere a los costos asociados con el trabajo necesario para producir bienes o servicios. Esto incluye no solo los salarios de los empleados directamente involucrados en la producción, sino también los beneficios y cargas sociales que la empresa debe pagar. La gestión adecuada de la mano de obra es esencial para mantener un equilibrio entre los costos y la productividad general.
Además, la capacitación y el desarrollo de habilidades de los trabajadores pueden incrementar la eficiencia y la calidad del producto final. Invertir en la formación de la mano de obra no solo mejora los resultados de producción, sino que también promueve un ambiente laboral más positivo y motivado. Por lo tanto, la mano de obra representa una parte crucial de los costos directos que las empresas deben gestionar cuidadosamente.
2.2 Costos Indirectos
Los costos indirectos son aquellos gastos que no se pueden atribuir directamente a un producto o servicio específico, pero que son necesarios para el funcionamiento general de la empresa. Estos costos incluyen elementos como el mantenimiento de las instalaciones, los servicios públicos y los salarios del personal administrativo. A pesar de no estar vinculados directamente a la producción, su gestión eficiente es fundamental para mantener un balance financiero saludable.
La correcta asignación de los costos indirectos puede ser un desafío, ya que requieren un análisis detallado para determinar su contribución a los diferentes productos o servicios. Estos costos son esenciales para calcular el costo total de producción y, en consecuencia, establecer precios competitivos en el mercado. Al optimizar la gestión de costos indirectos, las empresas pueden mejorar su rentabilidad general y asegurar un uso más eficiente de sus recursos.
2.2.1 Mantenimiento
El mantenimiento es un componente crucial de los costos indirectos, ya que asegura el buen funcionamiento de las instalaciones y equipos utilizados en la producción. Este gasto incluye actividades preventivas y correctivas, que ayudan a evitar fallos inesperados y prolongar la vida útil de los activos. Un programa de mantenimiento bien planificado no solo reduce los costos a largo plazo, sino que también mejora la eficiencia operativa.
Además, el mantenimiento adecuado contribuye a un ambiente de trabajo seguro y productivo, lo que es vital para el bienestar de los empleados. La falta de atención a los aspectos de mantenimiento puede resultar en interrupciones costosas en la producción y en una disminución de la calidad del producto. Por lo tanto, es esencial que las empresas integren el mantenimiento en su estrategia de gestión de costos indirectos.
2.2.2 Administración
Los costos de administración son otra categoría importante dentro de los costos indirectos, que incluyen todos los gastos relacionados con la gestión y operación de una empresa. Esto abarca salarios del personal administrativo, suministros de oficina y gastos de comunicación, entre otros. Una buena gestión de estos costos es esencial para asegurar que los recursos se utilicen de manera eficiente y efectiva.
La administración efectiva no solo contribuye al funcionamiento diario de la empresa, sino que también influye en la toma de decisiones estratégicas. Al analizar y optimizar los costos administrativos, las empresas pueden identificar áreas de mejora y reducir gastos innecesarios. Esto permite a las organizaciones mantener una estructura de costos competitiva y enfocarse en su crecimiento a largo plazo.
3. Estimación y Gestión de Costos
La estimación y gestión de costos son procesos esenciales para cualquier empresa que busque mantener su rentabilidad y competitividad en el mercado. La estimación implica predecir todos los costos asociados a un proyecto o línea de productos, lo que permite a las organizaciones establecer un presupuesto adecuado. Una estimación precisa ayuda a evitar sorpresas financieras y asegura que los recursos se asignen de manera eficiente y efectiva.
Por otro lado, la gestión de costos se refiere al seguimiento y control de los gastos durante el ciclo de vida del proyecto o proceso de producción. Implementar herramientas y técnicas de gestión permite a las empresas identificar rápidamente cualquier desviación de costos y tomar medidas correctivas. Esto no solo optimiza el uso de recursos, sino que también mejora la sostenibilidad financiera de la organización a largo plazo.
3.1 Técnicas de Estimación de Costos
Las técnicas de estimación de costos son herramientas fundamentales que permiten a las empresas prever sus gastos antes de iniciar un proyecto. Entre las más comunes se encuentran la estimación análoga, que utiliza datos de proyectos anteriores como referencia, y la estimación paramétrica, que se basa en relaciones matemáticas entre variables. Estas técnicas ayudan a establecer un presupuesto realista y a identificar posibles riesgos financieros desde el inicio.
Otra técnica valiosa es la estimación detallada, que implica desglosar cada componente del proyecto y calcular costos individuales de manera exhaustiva. Aunque esta técnica puede ser más laboriosa, ofrece un nivel de precisión superior que es esencial para proyectos complejos. Al adoptar estas técnicas de manera adecuada, las empresas pueden mejorar significativamente su capacidad de planificación financiera y gestión de recursos.
3.2 Importancia de la Gestión de Costos
La gestión de costos es crucial para el éxito financiero de cualquier empresa, ya que permite controlar y optimizar los gastos. Una buena gestión no solo ayuda a mantener el presupuesto dentro de los límites establecidos, sino que también proporciona información valiosa sobre el desempeño financiero de la organización. Esto facilita la identificación de áreas donde se pueden realizar mejoras y ajustes necesarios para maximizar la rentabilidad.
Además, la gestión de costos contribuye a la sostenibilidad a largo plazo de la empresa al garantizar que los recursos se utilicen de manera eficiente. Al tener un control riguroso sobre los gastos, las empresas pueden reaccionar rápidamente ante cualquier desviación y tomar decisiones informadas que impacten positivamente en su competitividad en el mercado. En un entorno empresarial dinámico, esta capacidad de adaptación es esencial para enfrentar desafíos y aprovechar oportunidades.
4. Ejemplos de Costos en la Industria Pesquera
En la industria pesquera, los costos de producción pueden variar significativamente dependiendo de diversos factores como la ubicación, el tipo de pesca y los métodos utilizados. Por ejemplo, los costos directos, como las materias primas y la mano de obra, son esenciales para calcular el costo total de producción de productos pesqueros. Además, los costos indirectos, que incluyen mantenimiento y administración, juegan un papel crucial en la gestión financiera de las empresas pesqueras.
Un ejemplo claro de cómo los costos afectan a la industria pesquera se observa en la variación de precios del hielo utilizado para conservar los productos. En países en desarrollo, los costos del hielo pueden ser considerablemente más altos, lo que impacta directamente en la rentabilidad de los pescadores. Al comprender estos costos y su impacto en el negocio, las empresas pueden tomar decisiones informadas para mejorar su eficiencia operativa y competitividad en el mercado.
4.1 Costos Directos en la Pesca
Los costos directos en la pesca son aquellos gastos que se pueden atribuir directamente a la captura de pescado y la producción de productos pesqueros. Esto incluye elementos como el combustible utilizado en las embarcaciones, las redes y equipos de pesca, así como la mano de obra necesaria para realizar la actividad. La correcta identificación y gestión de estos costos son esenciales para calcular el costo de producción y establecer precios competitivos en el mercado.
Además, los costos directos pueden fluctuar según las condiciones del mercado y la disponibilidad de recursos pesqueros. Por ejemplo, un aumento en el precio del combustible puede impactar significativamente los costos de operación de los pescadores. Al monitorear y controlar estos gastos, las empresas pesqueras pueden mejorar su rentabilidad y asegurar una operación más sostenible.
4.2 Costos Indirectos en la Industria Pesquera
Los costos indirectos en la industria pesquera abarcan una variedad de gastos que no se pueden atribuir directamente a la captura de pescado, pero que son esenciales para el funcionamiento del negocio. Estos costos incluyen el mantenimiento de embarcaciones, los salarios del personal administrativo y otros gastos operativos generales. Aunque a menudo se pasan por alto, su gestión adecuada es crucial para mantener la rentabilidad y eficiencia de las operaciones pesqueras.
Además, los costos indirectos pueden verse afectados por factores como la regulación ambiental y la necesidad de cumplir con normativas de sostenibilidad. Por ejemplo, las inversiones en tecnologías más limpias y prácticas de pesca sostenible pueden incrementar temporalmente los costos indirectos, pero a largo plazo pueden resultar en beneficios significativos. Al comprender y controlar estos costos, las empresas pesqueras pueden asegurar una operación más eficiente y responsable con el medio ambiente.
5. Relación entre Costos Fijos y Variables
La relación entre costos fijos y variables es fundamental para entender la estructura de costos de una empresa. Los costos fijos son aquellos que permanecen constantes independientemente del nivel de producción, como el alquiler de instalaciones y los salarios del personal administrativo. Por otro lado, los costos variables fluctúan en función de la producción, como los gastos en materiales y mano de obra directa, lo que significa que aumentan o disminuyen según la cantidad producida.
Comprender esta relación es crucial para la gestión financiera de una empresa, ya que permite a los gerentes tomar decisiones informadas sobre precios y producción. Un aumento en la producción puede reducir el costo variable por unidad, pero también es importante controlar los costos fijos para mantener la rentabilidad. Al equilibrar adecuadamente ambos tipos de costos, las empresas pueden mejorar su competitividad en el mercado y maximizar sus márgenes de beneficio.
5.1 Definición de Costos Fijos
Los costos fijos son aquellos gastos que permanecen constantes independientemente del nivel de producción o ventas de una empresa. Estos costos incluyen elementos como el alquiler de instalaciones, los salarios del personal administrativo y los seguros. Al no variar con la producción, los costos fijos proporcionan una base estable para la planificación financiera y el análisis de rentabilidad.
Aunque los costos fijos son esenciales para mantener las operaciones de una empresa, pueden representar un riesgo si las ventas disminuyen significativamente. Esto se debe a que, a diferencia de los costos variables, que se ajustan según la producción, los costos fijos deben pagarse incluso en períodos de baja actividad. Por lo tanto, es fundamental que las empresas gestionen sus costos fijos de manera eficiente para asegurar su viabilidad a largo plazo.
5.2 Definición de Costos Variables
Los costos variables son aquellos gastos que fluctúan en función del nivel de producción o ventas de una empresa. Estos costos incluyen elementos como la materia prima, la mano de obra directa y los costos de envío, que aumentan o disminuyen a medida que se produce más o menos. Debido a esta naturaleza cambiante, los costos variables son esenciales para entender la rentabilidad en diferentes niveles de producción.
Una característica importante de los costos variables es que permiten a las empresas ajustarse rápidamente a las condiciones del mercado. Si la demanda de un producto disminuye, los costos variables pueden reducirse al disminuir la producción, lo que ayuda a proteger la rentabilidad a corto plazo. Sin embargo, es crucial que las empresas mantengan un equilibrio entre costos fijos y variables para asegurar una gestión financiera saludable.
5.3 Impacto en la Rentabilidad Empresarial
El impacto en la rentabilidad empresarial de los costos fijos y variables es significativo, ya que ambos tipos de costos afectan el margen de utilidad. Los costos fijos, al ser constantes, pueden generar una presión adicional sobre las ganancias si las ventas disminuyen, mientras que los costos variables permiten a las empresas adaptarse a cambios en la demanda. Una gestión adecuada de ambos costos es esencial para mantener una rentabilidad sostenible.
Además, una alta proporción de costos fijos en comparación con los variables puede aumentar el riesgo financiero de la empresa. En escenarios de baja producción, los costos fijos continúan acumulándose, lo que puede llevar a pérdidas significativas. Por otro lado, un enfoque equilibrado en la gestión de costos fijos y variables puede ayudar a las empresas a maximizar su rentabilidad neta y a tener un mayor control sobre su viabilidad a largo plazo.
6. Consideraciones Finales sobre la Planificación Financiera
La planificación financiera es un proceso crucial que permite a las empresas establecer metas y estrategias para alcanzar sus objetivos económicos. Una planificación adecuada incluye la estimación de ingresos y gastos, así como la identificación de fuentes de financiamiento y la gestión de riesgos. Esto ayuda a las organizaciones a anticiparse a posibles desafíos y a tomar decisiones informadas que impacten positivamente en su salud financiera.
Además, la planificación financiera debe ser un proceso dinámico que se ajuste a las condiciones cambiantes del mercado y la economía. Es fundamental revisar y actualizar regularmente los planes para reflejar cambios en la operación, en la demanda del mercado y en la situación económica general. Al hacerlo, las empresas pueden asegurar una gestión más eficiente de recursos y una mayor capacidad de adaptación a los desafíos que puedan surgir.
6.1 Importancia de la Depreciación
La depreciación es un concepto esencial en la contabilidad que refleja la disminución del valor de los activos a lo largo del tiempo. Este proceso es crucial para calcular el costo real de operación de una empresa, ya que permite distribuir el costo de un activo a lo largo de su vida útil. Al reconocer la depreciación, las empresas pueden obtener una imagen más precisa de su rentabilidad y situación financiera.
Además, la depreciación tiene un impacto significativo en la planificación fiscal, ya que puede ser utilizada como un gasto deducible. Esto significa que las empresas pueden reducir su base imponible, lo que a su vez disminuye el monto de impuestos a pagar. Por lo tanto, una adecuada gestión de la depreciación no solo ayuda a reflejar el verdadero valor de los activos, sino que también contribuye a una mejor gestión financiera en general.
6.2 Otros Costos Asociados a la Producción
Además de los costos directos e indirectos, existen otros costos asociados a la producción que las empresas deben considerar para obtener una visión completa de sus gastos. Estos pueden incluir costos de investigación y desarrollo, gastos de marketing y costos de logística, que son fundamentales para llevar un producto al mercado. La inclusión de estos costos en el análisis financiero permite a las empresas tomar decisiones más informadas y estratégicas.
Asimismo, los costos asociados a la capacitación del personal y al mantenimiento de la calidad también juegan un papel importante en la producción. Invertir en la formación de los empleados no solo mejora la eficiencia, sino que también puede reducir costos a largo plazo al minimizar errores y desperdicios. Una adecuada gestión de todos estos costos es esencial para maximizar la rentabilidad y competitividad de la empresa en el mercado.
por PyMECity.es | 10-04-2025 | Calidad
Formación en PRL: Clave para líneas de producción seguras y eficientes
La formación en Prevención de Riesgos Laborales (PRL) es un componente esencial en cualquier línea de producción. Al capacitar a los empleados sobre los riesgos laborales y las mejores prácticas de seguridad, se pueden reducir significativamente los accidentes y crear un ambiente de trabajo más seguro. Esta formación no solo protege a los trabajadores, sino que también mejora la eficiencia operativa y la productividad general de la empresa.
Además, la automatización industrial juega un papel crucial en la modernización de las líneas de producción. Integrar tecnología avanzada puede ayudar a minimizar los riesgos, facilitando la identificación de peligros y la implementación de medidas de seguridad efectivas. La combinación de formación en PRL y tecnologías innovadoras asegura que las empresas puedan adaptarse a un entorno laboral en constante cambio, manteniendo altos estándares de seguridad y eficiencia.

1. La Importancia de la Formación en Prevención de Riesgos Laborales (PRL)
La formación en Prevención de Riesgos Laborales (PRL) es fundamental para garantizar la seguridad de los trabajadores en cualquier entorno industrial. Al proporcionar conocimientos sobre identificación de riesgos y prácticas seguras, se empodera a los empleados a actuar de manera proactiva. Esta capacitación no solo protege la salud de los trabajadores, sino que también contribuye a un ambiente laboral más productivo y eficiente.
Además, la formación en PRL fomenta una cultura de seguridad dentro de la organización. Cuando los empleados son conscientes de los riesgos y saben cómo mitigarlos adecuadamente, se reduce la probabilidad de accidentes y lesiones en el lugar de trabajo. Invertir en educación en PRL no solo es un deber legal, sino que también es una estrategia inteligente para mejorar el desempeño general de la empresa.
1.1. Objetivos de la Formación en PRL
Los principales objetivos de la formación en PRL son garantizar la seguridad y salud de los trabajadores en el entorno laboral. Esto se logra a través de la educación sobre riesgos, el uso adecuado de equipos de protección y la promoción de prácticas seguras. La capacitación también busca aumentar la conciencia sobre la prevención entre los empleados, lo que resulta en un ambiente de trabajo más seguro.
Otro objetivo clave es cumplir con las normativas legales que regulan la seguridad en el trabajo. La formación en PRL asegura que las empresas se adhieran a las leyes y regulaciones vigentes, evitando sanciones y mejorando su reputación. Además, al fomentar una cultura de prevención y responsabilidad, se contribuye a la sostenibilidad y éxito a largo plazo de la organización.
1.2. Impacto en la Seguridad Laboral
La formación en Prevención de Riesgos Laborales (PRL) tiene un impacto significativo en la seguridad laboral al reducir la tasa de accidentes y lesiones. Cuando los empleados están capacitados para identificar peligros y riesgos, pueden tomar decisiones informadas que protejan su bienestar. Esta educación no solo beneficia a los trabajadores, sino que también mejora la productividad general de la empresa al disminuir el tiempo perdido por incidentes.
Además, la implementación de programas de formación en PRL contribuye a crear una cultura de seguridad sólida dentro de la organización. Un entorno donde se prioriza la seguridad genera confianza y compromiso entre los empleados, lo que a su vez fomenta un clima laboral positivo. Esto puede traducirse en una mayor retención de talento y en un impacto favorable en la imagen corporativa de la empresa.
2. Automatización Industrial: Definición y Beneficios
La automatización industrial se refiere a la implementación de tecnologías y sistemas que controlan procesos de producción con mínima intervención humana. Este enfoque permite mejorar la eficiencia operativa al reducir los errores, aumentar la velocidad de producción y optimizar el uso de recursos. La automatización no solo transforma la manera en que se fabrican los productos, sino que también impacta positivamente en la calidad del producto final.
Entre los beneficios más destacados de la automatización se encuentra la reducción de costos a largo plazo. Al disminuir la dependencia de la mano de obra en tareas repetitivas, las empresas pueden redirigir sus recursos a áreas más creativas y estratégicas. Además, la automatización contribuye a un entorno de trabajo más seguro, ya que minimiza la exposición de los trabajadores a condiciones peligrosas y reduce la probabilidad de accidentes laborales.
2.1. ¿Qué es la Automatización Industrial?
La automatización industrial es el uso de tecnologías y sistemas para controlar y monitorizar procesos de producción sin intervención humana constante. Este enfoque implica la implementación de maquinaria, software y sensores que trabajan de manera conjunta para optimizar la producción. La automatización puede abarcar desde la robotización de tareas simples hasta sistemas complejos que gestionan toda una planta de producción.
Este proceso se fundamenta en la integración de tecnologías como el Internet de las Cosas (IoT) y la inteligencia artificial, que permiten una comunicación fluida entre dispositivos. A través de la automatización, las empresas pueden obtener datos en tiempo real sobre su producción, lo que les ayuda a tomar decisiones informadas y mejorar la eficiencia operativa. Además, la automatización industrial se adapta a diferentes sectores, desde la manufactura hasta la industria alimentaria, cada uno con sus necesidades específicas.
2.2. Beneficios de la Automatización en Líneas de Producción
La automatización en líneas de producción ofrece una serie de beneficios significativos que mejoran la competitividad de las empresas. Uno de los principales beneficios es la incremento de la eficiencia, ya que las máquinas pueden trabajar de manera continua, reduciendo los tiempos de inactividad. Esto permite que las empresas produzcan más en menos tiempo, optimizando el uso de recursos y aumentando la capacidad de producción.
Otro beneficio importante es la mejora en la calidad del producto. La automatización reduce la variabilidad en el proceso de producción, lo que resulta en productos más consistentes y de mayor calidad. Además, al minimizar la intervención humana en tareas repetitivas, se disminuye el riesgo de errores y defectos, lo que contribuye a una mayor satisfacción del cliente y a una mejor reputación en el mercado.
2.2.1. Mejora de la Productividad
La automatización en las líneas de producción juega un papel crucial en la mejora de la productividad general de una empresa. Al integrar sistemas automatizados, las tareas se realizan de manera más rápida y eficiente, lo que permite a las empresas aumentar su producción diaria sin necesidad de incrementar significativamente los costos. Esta capacidad de escalar rápidamente es fundamental para satisfacer la demanda del mercado y permanecer competitivos.
Además, la automatización reduce el tiempo dedicado a tareas manuales y repetitivas, permitiendo que los empleados se enfoquen en actividades de mayor valor. Esto no solo optimiza el uso del capital humano, sino que también fomenta un entorno en el que se pueden implementar mejoras continuas y nuevas innovaciones. Por lo tanto, la automatización se convierte en una herramienta clave para maximizar la eficiencia y los resultados de producción.
2.2.2. Reducción de Riesgos Laborales
La automatización en las líneas de producción contribuye significativamente a la reducción de riesgos laborales. Al reemplazar tareas peligrosas o físicamente exigentes con máquinas, se minimiza la exposición de los empleados a situaciones que podrían resultar en lesiones o accidentes. Esto no solo protege la salud de los trabajadores, sino que también mejora la moral del equipo al crear un entorno de trabajo más seguro.
Además, al implementar sistemas automatizados, se pueden establecer protocolos de seguridad más rigurosos y eficientes. Las máquinas pueden ser programadas para seguir normas de seguridad estrictas, lo que garantiza que se mantenga un control constante sobre los procesos de producción. Esta mejora en la seguridad laboral permite a las empresas enfocarse en el crecimiento y la innovación, sin las distracciones que causan los accidentes laborales.
3. Elementos Clave en el Diseño de Líneas de Producción
El diseño de líneas de producción es fundamental para garantizar un flujo de trabajo eficiente y seguro. Entre los elementos clave se encuentran la disposición de las estaciones de trabajo, el tipo de maquinaria utilizada y la ergonomía aplicada en el espacio laboral. Una planificación adecuada de estos factores puede maximizar la productividad y minimizar los tiempos de inactividad, lo que resulta en un proceso de producción más fluido.
Además, es esencial considerar la flexibilidad del diseño para adaptarse a cambios en la demanda o en los productos fabricados. Las líneas de producción deben ser capaces de ajustarse rápidamente a nuevas configuraciones sin comprometer la eficiencia. También es importante incluir sistemas de monitoreo y control que permitan a los administradores evaluar el rendimiento en tiempo real y realizar ajustes cuando sea necesario.
3.1. Análisis de Procesos
El análisis de procesos es una herramienta esencial en el diseño de líneas de producción, ya que permite identificar ineficiencias y áreas de mejora. Este proceso implica examinar cada etapa de la producción para entender cómo fluyen los materiales y la información. Al realizar un análisis exhaustivo, las empresas pueden optimizar sus operaciones y reducir los costos operativos.
Además, el análisis de procesos facilita la identificación de cuellos de botella que pueden ralentizar la producción. Con esta información, es posible implementar soluciones específicas que mejoren el rendimiento general de la línea. Asimismo, el análisis continuo de los procesos permite a las empresas adaptarse a las cambios en el mercado y a las necesidades del cliente, garantizando una operación más ágil y competitiva.
3.2. Ergonomía en el Diseño
La ergonomía en el diseño de líneas de producción es fundamental para asegurar la salud y el bienestar de los trabajadores. Este enfoque busca adaptar el entorno laboral a las capacidades y limitaciones humanas, minimizando el riesgo de lesiones y aumentando la satisfacción laboral. Al considerar factores como la postura, el alcance y el movimiento, se pueden crear espacios de trabajo más cómodos y eficientes.
Implementar principios ergonómicos no solo mejora la comodidad de los empleados, sino que también puede aumentar la productividad general. Un diseño ergonómico reduce la fatiga y el estrés físico, lo que permite a los trabajadores mantener un rendimiento óptimo a lo largo de la jornada. Además, invertir en ergonomía puede disminuir las ausencias laborales causadas por lesiones, lo que se traduce en beneficios económicos para la empresa.
4. Accidentes Comunes en Líneas de Producción
Las líneas de producción, a pesar de su eficiencia, pueden ser escenarios de accidentes laborales si no se gestionan adecuadamente. Entre los accidentes más comunes se encuentran las caídas, atrapamientos y golpes por objetos en movimiento. Estos incidentes no solo ponen en riesgo la salud de los trabajadores, sino que también pueden interrumpir el flujo de producción y generar costos adicionales para la empresa.
Otro tipo de accidente frecuente en las líneas de producción es la lesión por esfuerzo repetitivo, que puede afectar a los trabajadores que realizan tareas manuales de forma continua. Este tipo de lesiones suele ser silencioso, desarrollándose con el tiempo y afectando la calidad de vida de los empleados. Además, la falta de capacitación en el uso de equipos de seguridad puede aumentar la probabilidad de sufrir accidentes graves, lo que resalta la importancia de la formación en Prevención de Riesgos Laborales.
4.1. Tipos de Accidentes
Existen varios tipos de accidentes que pueden ocurrir en las líneas de producción, cada uno con sus propias causas y consecuencias. Los accidentes más comunes incluyen caídas, que pueden suceder por superficies resbaladizas o mal mantenidas, y golpes por objetos que caen, que a menudo son el resultado de una incorrecta manipulación de materiales. Estos incidentes no solo afectan la salud de los trabajadores, sino que también pueden ocasionar pérdidas significativas en la productividad.
Otro tipo de accidente frecuente es el atrapamiento, que ocurre cuando una parte del cuerpo queda atrapada entre maquinaria o equipos. Este tipo de accidente puede ser extremadamente grave y requiere de una atención meticulosa en la capacitación y el uso de equipos de protección personal adecuados. Además, las lesiones por esfuerzo repetitivo, aunque menos visibles, son igualmente preocupantes ya que pueden desarrollarse con el tiempo y afectar la capacidad de los trabajadores para realizar sus tareas diarias.
4.2. Consecuencias de los Accidentes en el Trabajo
Los accidentes en el trabajo pueden tener consecuencias devastadoras tanto para los empleados como para las empresas. En el ámbito personal, las lesiones pueden resultar en licencias médicas prolongadas, lo que genera una pérdida de ingresos y una posible disminución de la calidad de vida del afectado. Además, los accidentes pueden provocar estrés emocional y ansiedad, afectando la salud mental de los trabajadores involucrados.
Desde la perspectiva empresarial, los accidentes laborales pueden llevar a un aumento en los costos operativos debido a los gastos médicos y las compensaciones por lesiones. También pueden resultar en una reducción de la productividad, ya que los empleados pueden sentirse inseguros en su entorno de trabajo después de un incidente. Por último, las empresas pueden enfrentar un daño a su reputación y la pérdida de confianza de los clientes, lo que puede tener un impacto negativo en su rentabilidad a largo plazo.
5. Medidas Preventivas para Aumentar la Seguridad
Implementar medidas preventivas es esencial para aumentar la seguridad en el trabajo y proteger a los empleados de posibles riesgos. Entre estas medidas se incluyen la capacitación regular en Prevención de Riesgos Laborales, que asegura que todos los trabajadores conozcan los procedimientos adecuados para manejar situaciones peligrosas. Además, el uso de Equipos de Protección Individual (EPIs) es fundamental para minimizar la exposición a riesgos físicos y químicos en el entorno laboral.
La realización de auditorías de seguridad y el mantenimiento regular de la maquinaria también son prácticas clave para prevenir accidentes. Estas auditorías permiten identificar áreas de mejora y asegurar que todos los equipos cumplan con los estándares de seguridad necesarios. Un entorno de trabajo bien mantenido y seguro no solo protege a los empleados, sino que también mejora la productividad general de la empresa.
5.1. Capacitación en PRL
La capacitación en Prevención de Riesgos Laborales (PRL) es crucial para equipar a los empleados con los conocimientos necesarios para identificar y manejar riesgos en el entorno laboral. Este tipo de formación abarca temas como la identificación de peligros, el uso correcto de Equipos de Protección Individual (EPIs) y las mejores prácticas de seguridad. Al recibir formación adecuada, los trabajadores se sienten más seguros y capacitados para actuar en situaciones de riesgo.
Además, la capacitación en PRL no solo protege a los empleados, sino que también beneficia a la empresa al reducir la tasa de accidentes y las correspondientes pérdidas económicas. Los programas de formación deben ser actualizados regularmente para reflejar los cambios en la legislación y las nuevas tecnologías. Invertir en la capacitación de PRL es una estrategia inteligente que contribuye a crear un ambiente de trabajo más seguro y eficiente.
5.2. Uso de Equipos de Protección Individual (EPIs)
El uso de Equipos de Protección Individual (EPIs) es fundamental para salvaguardar la salud y seguridad de los trabajadores en entornos industriales. Estos equipos incluyen elementos como cascos, guantes, gafas de seguridad y ropa de protección, diseñados específicamente para minimizar la exposición a riesgos. Al utilizar los EPIs adecuados, los empleados pueden desempeñar sus tareas con una mayor tranquilidad y confianza.
Es crucial que las empresas no solo proporcionen EPIs, sino que también capaciten a los trabajadores en su uso correcto y mantenimiento. Una adecuada formación sobre cómo utilizar estos equipos puede reducir significativamente el riesgo de lesiones laborales y mejorar la efectividad de su protección. Además, garantizar que los EPIs estén en buen estado y sean apropiados para el trabajo específico es vital para maximizar su eficacia y funcionalidad.
6. Tecnología como Aliado en la Seguridad y Eficiencia
La integración de la tecnología en los procesos de producción se ha convertido en un aliado clave para mejorar tanto la seguridad como la eficiencia en el trabajo. Herramientas como la inteligencia artificial y el Internet de las Cosas (IoT) permiten a las empresas monitorear en tiempo real las condiciones de trabajo y detectar posibles riesgos antes de que se conviertan en problemas. Esta capacidad de anticipación no solo protege a los empleados, sino que también optimiza el flujo de trabajo al reducir tiempos de inactividad.
Además, los sistemas automatizados pueden realizar tareas repetitivas y peligrosas, liberando a los empleados de trabajos que podrían poner en riesgo su seguridad. Al implementar tecnologías avanzadas, las empresas pueden crear un entorno laboral más seguro y adaptativo, donde se prioriza el bienestar del empleado. La digitalización de procesos también facilita la capacitación continua, asegurando que todos los trabajadores estén al tanto de las mejores prácticas de seguridad y del uso correcto de equipos y herramientas.
6.1. Aplicaciones Tecnológicas en la Prevención de Accidentes
Las aplicaciones tecnológicas en la prevención de accidentes han revolucionado la forma en que las empresas gestionan la seguridad laboral. Herramientas como sistemas de monitoreo en tiempo real y sensores de movimiento permiten identificar comportamientos de riesgo antes de que ocurran incidentes. Estas tecnologías proporcionan alertas inmediatas, lo que ayuda a los trabajadores a tomar decisiones informadas y a mantenerse seguros en su entorno laboral.
Además, las plataformas de formación virtual y simuladores de realidad aumentada ofrecen a los empleados la oportunidad de aprender sobre prácticas de seguridad en un entorno controlado. Estas herramientas permiten a los trabajadores experimentar situaciones de riesgo sin estar expuestos a peligros reales, mejorando su preparación para enfrentar desafíos en el trabajo. La integración de tecnología en la formación y prevención no solo aumenta la eficacia de los programas de seguridad, sino que también fomenta una cultura organizacional más consciente de los riesgos.
6.2. Futuro de la Seguridad Laboral con Tecnología
El futuro de la seguridad laboral está cada vez más ligado a la evolución de la tecnología avanzada. Innovaciones como la inteligencia artificial y el análisis de datos permitirán a las empresas predecir y prevenir accidentes mediante la identificación de patrones de riesgo. A medida que estas tecnologías se integren en la cultura organizacional, se espera que la eficacia de las medidas de seguridad aumente considerablemente.
Además, el uso de dispositivos portátiles y wearables permitirá a los trabajadores monitorear su salud y seguridad en tiempo real. Estos dispositivos pueden detectar condiciones peligrosas, como exposición a gases tóxicos o niveles de fatiga, alertando al usuario y a los supervisores antes de que se produzca un accidente. La combinación de estas herramientas tecnológicas no solo transformará el enfoque hacia la seguridad laboral, sino que también promoverá un entorno de trabajo más proactivo y consciente de los riesgos.
por PyMECity.es | 02-04-2025 | Producción
Optimiza tus Costos de Producción y Aumenta tu Rentabilidad
Optimizar los costos de producción es esencial para cualquier empresa que busque mejorar su salud financiera. Al clasificar los costos en variables y fijos, se pueden identificar áreas donde se puede reducir el gasto sin comprometer la calidad. Este enfoque no solo ayuda a mantener los márgenes de ganancia, sino que también permite una toma de decisiones más informada.
Calcular el costo total de producción implica considerar elementos como materia prima, mano de obra y otros gastos asociados. La implementación de tecnologías avanzadas puede facilitar este proceso, permitiendo un control más preciso de los costos y una gestión más eficiente de los recursos. Herramientas específicas, como las de TOTVS, son fundamentales para optimizar procesos y mejorar los resultados en la industria.

1. Introducción a los Costos de Producción
Los costos de producción son una parte fundamental de cualquier negocio, ya que representan todos los gastos asociados a la fabricación de bienes o servicios. Comprender estos costos es esencial para garantizar la rentabilidad a largo plazo de la empresa. Al clasificar los costos en fijos y variables, las organizaciones pueden identificar oportunidades para mejorar la eficiencia y reducir gastos.
La correcta gestión de los costos de producción permite a las empresas establecer precios competitivos y maximizar sus márgenes de ganancia. Además, conocer los costos ayuda a los gerentes a tomar decisiones informadas sobre inversiones y estrategias de crecimiento sostenible. En un entorno empresarial cada vez más competitivo, dominar esta área se convierte en una ventaja crucial para el éxito.
1.1 Importancia de los Costos de Producción en la Empresa
La importancia de los costos de producción radica en su impacto directo sobre la salud financiera de una empresa. Estos costos no solo determinan el precio de venta de los productos, sino que también afectan la competitividad en el mercado. Un control adecuado de los costos permite a las empresas ajustar su estrategia y responder a las dinámicas del entorno económico.
Además, entender los costos de producción ayuda a identificar áreas donde se pueden realizar mejoras significativas en la eficiencia operativa. Esto no solo se traduce en una reducción de gastos, sino que también puede resultar en un uso más efectivo de los recursos disponibles. En un mundo empresarial donde cada centavo cuenta, la gestión de costos se convierte en una herramienta clave para optimizar recursos y maximizar beneficios.
1.2 Clasificación de Costos: Fijos y Variables
La clasificación de costos en fijos y variables es fundamental para la gestión financiera de una empresa. Los costos fijos son aquellos que no cambian con el nivel de producción, como el alquiler de locales o los salarios de empleados permanentes. Por otro lado, los costos variables fluctúan directamente con la producción, incluyendo gastos como materia prima y comisiones de ventas.
Comprender esta clasificación permite a las empresas realizar análisis más precisos y tomar decisiones informadas sobre sus operaciones. Por ejemplo, al conocer sus costos fijos, una empresa puede establecer un nivel mínimo de producción necesario para cubrir sus gastos. Asimismo, la identificación de costos variables ayuda a evaluar el impacto de cambios en la producción sobre la rentabilidad general.
2. Cálculo del Costo Total de Producción
El cálculo del costo total de producción es un proceso esencial que ayuda a las empresas a entender sus gastos operativos. Este costo incluye componentes como la materia prima, la mano de obra directa y los costos indirectos asociados a la fabricación. Al tener una visión clara de estos elementos, las empresas pueden fijar precios de venta adecuados y asegurar su rentabilidad.
Para calcular el costo total de producción, es importante sumar todos los costos relacionados con la producción de bienes o servicios. Esto implica no solo considerar los costos directos, sino también los gastos fijos y variables que afectan la operación diaria. Un análisis detallado de estos costos permite a las organizaciones identificar áreas de optimización y mejorar su eficiencia general.
2.1 Componentes del Costo Total
Los componentes del costo total de producción son cruciales para obtener una visión clara de los gastos de una empresa. Entre ellos, la materia prima representa uno de los costos más significativos, ya que incluye todos los materiales necesarios para fabricar un producto. Además, es esencial considerar la mano de obra, que abarca los salarios de los empleados directamente involucrados en el proceso de producción.
Otro componente importante son los costos indirectos, que incluyen gastos generales como alquiler, servicios públicos y mantenimiento de equipos. Estos costos pueden parecer menores en comparación con los directos, pero pueden acumularse rápidamente y afectar la rentabilidad. Al entender y desglosar estos componentes, las empresas pueden tomar decisiones más informadas sobre la producción y la gestión de recursos.
2.1.1 Materia Prima
La materia prima es uno de los elementos más críticos en el cálculo del costo total de producción. Se refiere a los materiales básicos utilizados en la fabricación de productos, que pueden incluir desde metales y plásticos hasta ingredientes alimentarios. La gestión eficiente de la materia prima no solo impacta en los costos, sino que también puede influir en la calidad del producto final.
Además, el precio de la materia prima puede fluctuar debido a factores como la oferta y la demanda, así como a condiciones económicas globales. Por ello, las empresas deben estar atentas a las tendencias del mercado y establecer acuerdos con proveedores para asegurar un suministro constante y a buen precio. Un control adecuado sobre la materia prima permite a las organizaciones optimizar sus procesos de producción y mejorar su competitividad.
2.1.2 Mano de Obra
La mano de obra es un componente esencial en el costo total de producción, ya que incluye los salarios y beneficios de los trabajadores directamente involucrados en el proceso de fabricación. Este costo puede variar según la habilidad y experiencia de los empleados, así como por el tipo de trabajo que realicen. Invertir en mano de obra calificada puede mejorar significativamente la eficiencia productiva y la calidad del producto final.
Además de los salarios, la mano de obra incluye costos adicionales como horas extras, capacitación y seguros. Las empresas deben equilibrar estos gastos con la necesidad de mantener un equipo motivado y comprometido. Un manejo adecuado de los costos de mano de obra es crucial para maximizar la rentabilidad y asegurar el éxito a largo plazo del negocio.
2.1.3 Otros Gastos Asociados
Los otros gastos asociados son aquellos costos que no se clasifican directamente como materia prima o mano de obra, pero que son igualmente importantes para la producción. Estos pueden incluir gastos de mantenimiento de maquinaria, costos de energía y servicios públicos, así como seguros y alquileres de instalaciones. Aunque pueden parecer menores en comparación con otros costos, su acumulación puede impactar significativamente en la rentabilidad general de la empresa.
La gestión eficiente de estos gastos requiere un monitoreo constante y una planificación cuidadosa. Por ejemplo, implementar prácticas de mantenimiento preventivo puede reducir costos inesperados en reparaciones de maquinaria. Además, optimizar el uso de recursos energéticos no solo ayuda a controlar costos, sino que también contribuye a la sostenibilidad del negocio.
3. Diferencia entre Costos Contables y Económicos
La diferencia entre costos contables y económicos es fundamental para entender cómo se gestionan las finanzas de una empresa. Los costos contables son aquellos que se registran en los libros contables y se centran en los gastos reales incurridos en un período determinado. Por otro lado, los costos económicos consideran no solo los costos explícitos, sino también los costos de oportunidad, que representan los beneficios perdidos al elegir una opción sobre otra.
Comprender esta distinción es crucial para la toma de decisiones empresariales informadas. Mientras que los costos contables ayudan a evaluar la rentabilidad y el desempeño financiero a corto plazo, los costos económicos ofrecen una perspectiva más amplia sobre la viabilidad a largo plazo de las inversiones. Así, una empresa puede evaluar no solo qué gastos incurre, sino también qué alternativas podría haber tomado para maximizar sus beneficios.
3.1 Definición de Costos Contables
Los costos contables se refieren a los gastos que una empresa registra en sus libros contables durante un período específico. Estos costos son fundamentales para la elaboración de informes financieros y la evaluación del desempeño económico de la organización. Incluyen elementos como materiales, mano de obra y otros gastos directos que se relacionan con la producción de bienes o servicios.
Una característica clave de los costos contables es que son fácilmente cuantificables y se basan en transacciones reales. Esto permite a las empresas realizar un seguimiento preciso de sus gastos operativos y preparar estados financieros que reflejen su situación económica. Además, los costos contables son esenciales para el cumplimiento de normativas fiscales y contables, asegurando la transparencia en la presentación de información financiera.
3.2 Definición de Costos Económicos
Los costos económicos son una medida más amplia que incluye no solo los gastos directos de producción, sino también los costos de oportunidad asociados a decisiones empresariales. Estos costos reflejan el valor de los recursos que se utilizan en una opción en lugar de en otra, lo que implica considerar qué beneficios se pierden al elegir un camino específico. Por ejemplo, al invertir en un proyecto, una empresa debe tener en cuenta no solo la inversión inicial, sino también los ingresos potenciales que se podrían haber generado en alternativas no elegidas.
Una de las ventajas de analizar los costos económicos es que proporciona una visión más completa de la efectividad de las decisiones estratégicas. Al entender los costos económicos, las empresas pueden evaluar mejor el impacto de sus inversiones y estrategias comerciales en la rentabilidad a largo plazo. Esta perspectiva integral ayuda a los gerentes a tomar decisiones más informadas, optimizando el uso de recursos y maximizando el rendimiento de las inversiones.
4. Estrategias para Gestionar Eficientemente los Costos
Gestionar eficientemente los costos es fundamental para la salud financiera de cualquier empresa. Una estrategia clave es implementar un monitoreo constante de gastos, lo que permite identificar áreas donde se pueden realizar ajustes y optimizaciones. Herramientas de análisis financiero pueden ser de gran ayuda para visualizar tendencias en los gastos y detectar posibles sobrecostos de manera oportuna.
Otra estrategia efectiva es la negociación con proveedores para obtener mejores precios y condiciones. Establecer relaciones sólidas con los proveedores puede resultar en descuentos por volumen o condiciones de pago más favorables, lo que a su vez mejora la gestión del flujo de caja. Además, fomentar una cultura de conciencia de costos entre los empleados puede contribuir a la reducción de gastos innecesarios y promover un ambiente de trabajo más eficiente.
4.1 Identificación de Áreas de Mejora
La identificación de áreas de mejora es un paso crucial en la gestión de costos, ya que permite a las empresas optimizar sus recursos. Este proceso implica realizar un análisis detallado de los gastos actuales y evaluar la eficiencia de cada departamento. Identificar los gastos innecesarios o redundantes ayuda a concentrarse en las áreas que requieren atención inmediata y pueden generar ahorros significativos.
Una manera efectiva de identificar estas áreas es a través de la recopilación de datos y el uso de indicadores de rendimiento. Herramientas de análisis de datos pueden proporcionar información valiosa sobre patrones de gasto y áreas donde se pueden implementar mejoras. Al tener una visión clara de los puntos débiles, las empresas pueden establecer prioridades para las estrategias de reducción de costos y aplicar cambios que impacten positivamente en su rentabilidad.
4.2 Implementación de Herramientas de Gestión
La implementación de herramientas de gestión es esencial para mejorar la eficiencia en el control de costos. Estas herramientas pueden incluir software de planificación de recursos empresariales (ERP), que facilitan la integración de datos y procesos en toda la organización. La automatización de tareas administrativas permite a las empresas dedicar más tiempo a actividades estratégicas, optimizando así el uso de recursos y reduciendo costos operativos.
Además, las herramientas de gestión ofrecen la posibilidad de realizar un seguimiento en tiempo real de los gastos y el rendimiento financiero. Esto permite a los gerentes tomar decisiones informadas basadas en datos actualizados, lo que mejora la capacidad de respuesta ante cambios en el mercado. La capacitación adecuada en el uso de estas herramientas es fundamental para asegurar que el personal pueda utilizarlas eficientemente y maximizar su potencial de ahorro.
5. La Tecnología como Aliada en la Gestión de Costos
La tecnología se ha convertido en un aliado esencial en la gestión de costos, proporcionando herramientas que mejoran la eficiencia operativa. Las soluciones de software permiten un análisis detallado de los gastos, así como la automatización de procesos que antes requerían una gran cantidad de tiempo y recursos. Al implementar estas tecnologías, las empresas pueden reducir errores y optimizar el uso de recursos, lo que se traduce en ahorros significativos.
Además, la tecnología facilita la recopilación y el análisis de datos, lo que permite a las organizaciones tomar decisiones más informadas. Herramientas como plataformas de análisis de datos y sistemas de gestión de inventarios ayudan a identificar tendencias de gasto y áreas donde se pueden realizar mejoras. Esta capacidad de respuesta ante datos actualizados no solo optimiza la gestión de costos, sino que también mejora la competitividad en el mercado.
5.1 Soluciones Tecnológicas Disponibles
Existen diversas soluciones tecnológicas disponibles que pueden ayudar a las empresas a gestionar sus costos de manera más eficiente. Por ejemplo, los sistemas de planificación de recursos empresariales (ERP) integran todas las funciones de negocio en una única plataforma, permitiendo un flujo de información más efectivo entre departamentos. Esto no solo mejora la precisión en la contabilidad, sino que también permite un control más riguroso de los gastos operativos.
Otra solución valiosa son las herramientas de análisis de datos, que permiten a las empresas visualizar patrones de gasto y rendimiento con mayor claridad. Estas herramientas facilitan la identificación de áreas donde se pueden realizar ajustes significativos, ayudando a las organizaciones a tomar decisiones informadas. Además, las aplicaciones de gestión de inventarios permiten un seguimiento en tiempo real, optimizando el uso de los recursos y minimizando los costos innecesarios.
5.1.1 Herramientas de TOTVS
Las herramientas de TOTVS son soluciones tecnológicas diseñadas específicamente para ayudar a las empresas a optimizar su gestión de costos y recursos. Estas herramientas incluyen sistemas de gestión empresarial que integran diversas funciones, como finanzas, compras y producción, en una única plataforma. Esto permite un flujo de información eficiente y una mejor toma de decisiones basadas en datos precisos y actualizados.
Además, las soluciones de TOTVS ofrecen funcionalidades avanzadas de análisis y reporte que permiten a las empresas visualizar sus gastos y rendimiento en tiempo real. Con estas herramientas, los gerentes pueden identificar rápidamente tendencias de gasto y áreas que requieren atención, facilitando así la implementación de estrategias de reducción de costos. La capacidad de personalizar estas herramientas según las necesidades específicas de cada negocio también aumenta su efectividad en la gestión.
5.2 Beneficios de la Automatización de Procesos
La automatización de procesos ofrece múltiples beneficios que pueden transformar la gestión de costos en una empresa. Al automatizar tareas repetitivas y administrativas, las organizaciones pueden liberar tiempo valioso para que los empleados se concentren en actividades más estratégicas y creativas. Esto no solo aumenta la productividad general, sino que también reduce la posibilidad de errores humanos, lo que a su vez disminuye costos adicionales.
Además, la automatización permite un seguimiento más preciso y en tiempo real de los gastos y recursos. Esto facilita la toma de decisiones informadas basadas en datos actualizados, lo que contribuye a una mejor planificación y control de costos. Al implementar herramientas automatizadas, las empresas pueden lograr una mayor eficiencia operativa y, en última instancia, mejorar su rentabilidad a largo plazo.
6. Conclusiones y Recomendaciones Finales
La gestión de costos es un aspecto crítico que puede determinar el éxito de una empresa en el competitivo mundo actual. Implementar estrategias efectivas para el control de costos, como la identificación de áreas de mejora y la adopción de herramientas tecnológicas, puede resultar en ahorros significativos y en una mejor rentabilidad. Además, la automatización de procesos no solo aumenta la eficiencia operativa, sino que también reduce la posibilidad de errores, lo que se traduce en un manejo más efectivo de los recursos.
Es fundamental que las empresas mantengan una mentalidad proactiva en la gestión de sus costos, adaptándose a los cambios del mercado y aprovechando las nuevas tecnologías. La capacitación continua del personal en el uso de herramientas de gestión y análisis también es crucial para maximizar los beneficios. Al hacerlo, las organizaciones pueden asegurar un futuro sostenible y rentable, alineando sus objetivos económicos con las mejores prácticas del sector.
6.1 Resumen de Puntos Clave
Un aspecto fundamental en la gestión de costos es la clasificación adecuada de los mismos, diferenciando entre costos fijos y variables. Esto permite a las empresas entender mejor su estructura de gastos y ajustar sus estrategias de producción y precios en consecuencia. Además, tener claridad sobre los componentes del costo total ayuda a identificar áreas de optimización que pueden generar ahorros significativos.
La tecnología juega un papel crucial en la gestión de costos, ofreciendo soluciones automatizadas que facilitan el seguimiento y análisis de gastos. Herramientas como sistemas ERP y software de análisis de datos permiten un control más riguroso y una toma de decisiones basada en información precisa. Por último, la capacitación del personal y la implementación de una cultura de conciencia de costos son esenciales para lograr una gestión eficiente y sostenible a largo plazo.
6.2 Pasos a Seguir para Mejorar la Rentabilidad
Para mejorar la rentabilidad, el primer paso es realizar un análisis exhaustivo de los costos operativos y determinar cuáles son necesarios y cuáles pueden ser reducidos. Esto implica identificar áreas de desperdicio y optimizar el uso de recursos, lo que puede llevar a una reducción significativa de gastos. Además, es vital revisar periódicamente los precios de los productos o servicios para asegurarse de que estén alineados con el mercado y cubran adecuadamente los costos.
Otro paso importante es implementar tecnología que facilite la automatización de procesos, lo que no solo mejora la eficiencia, sino que también reduce la probabilidad de errores. Capacitar al personal en el uso de estas herramientas es esencial para maximizar su potencial y asegurar que todos estén alineados con los objetivos de reducción de costos. Finalmente, fomentar una cultura de innovación y mejora continua ayudará a las empresas a adaptarse a los cambios del mercado y a buscar constantemente nuevas formas de aumentar su rentabilidad.